Basic Info.
Model NO.
BWJ
Condition
New
Model
Bwj
Positioner Function
Dual Axis Robotic Welding Rotary Positioner
Loading Weight
200kg
Rotary Table Size
500mm
Rotating Speed of Table
12.5 Rpm/Min
Tilt Angle
90 Degree
Reducer Type
RV Reducer
Servo Motor
1.5kw
Robot Brand
Kuka,Funuc etc.
Lead Time
30 Days
Height Adjustment
Customized
Length Adjustment
Customized
Exported to
Europe,USA,UK,Russia etc
Warranty
1 Year
Radius of Gyration
400mm
Transport Package
Wooden
Trademark
Lemar
Origin
Wuxi, China
HS Code
8428909090
Packaging & Delivery
Package Size
50.00cm * 50.00cm * 120.00cm
Package Gross Weight
260.000kg
Product Description
200kg 500mm Welding table diameter Rotary welding turntable for Robot
Robot welding positioners mostly use RV series worm gear reducers, or even conjoined RV worm gear reducers, as reduction devices.
Its advantages are stable output and stable structure.
The dual-axis positioner is a common welding auxiliary equipment. Its main function is to realize the rotation and displacement of the workpiece during the welding process, so as to obtain a good welding position.
The double-axis P-type positioner is generally welded by profiles and steel plates. After annealing, the quality is reliable. Using motor drive and high-precision reducer, the rotation or turning speed can be adjusted.
Robot welding positioners mostly use RV series worm gear reducers, or even conjoined RV worm gear reducers, as reduction devices.
Its advantages are stable output and stable structure.
The dual-axis positioner is a common welding auxiliary equipment. Its main function is to realize the rotation and displacement of the workpiece during the welding process, so as to obtain a good welding position.
The double-axis P-type positioner is generally welded by profiles and steel plates. After annealing, the quality is reliable. Using motor drive and high-precision reducer, the rotation or turning speed can be adjusted.
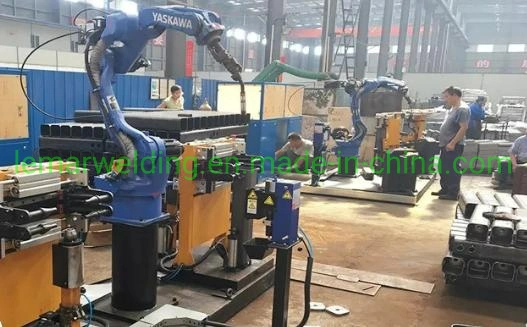
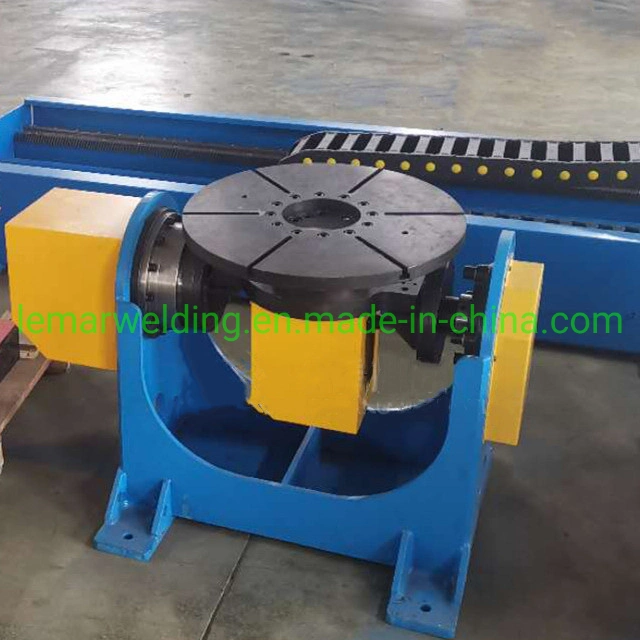
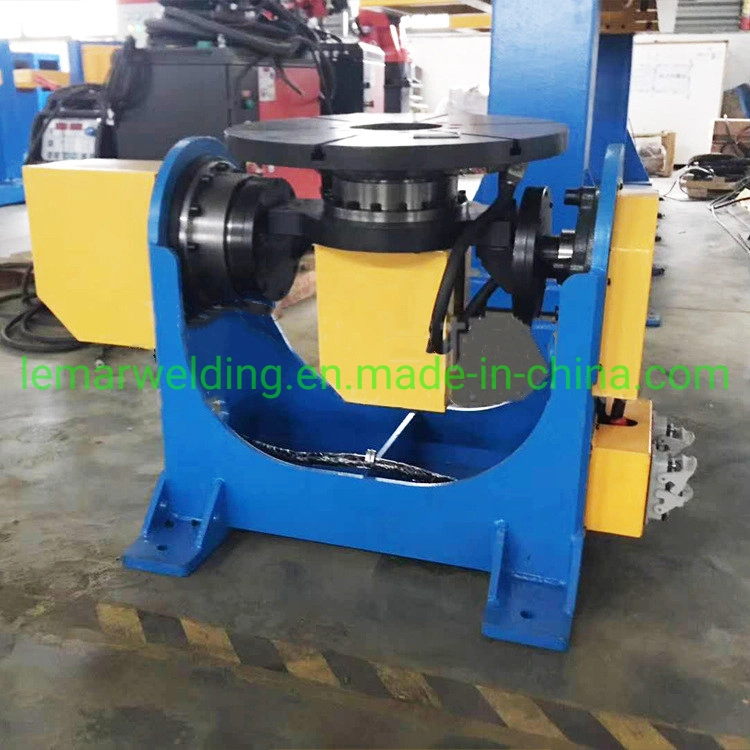
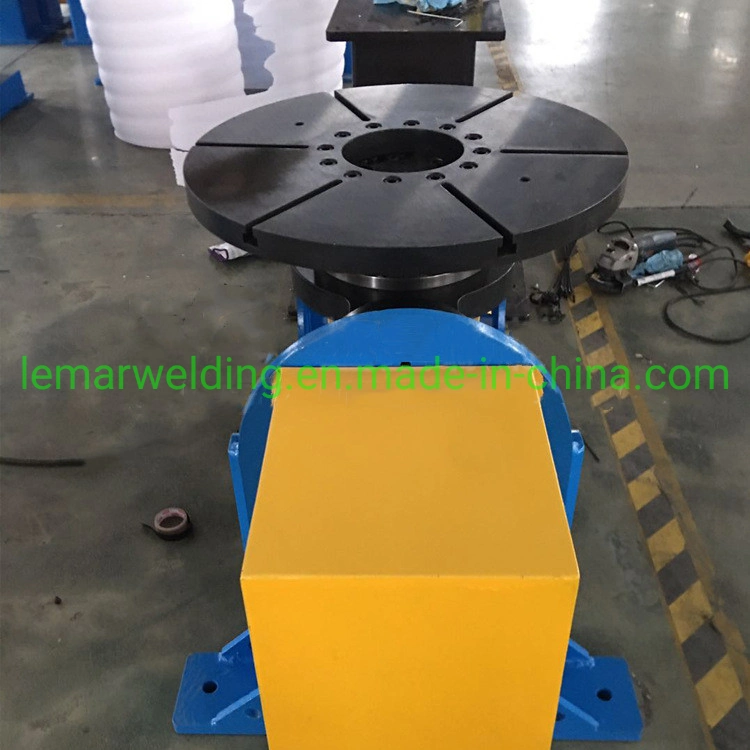
Specification of Dual axis automatic turning table Robot welding positioner:
Model | BWJ-100 | BWJ-200 | BWJ-300 | BWJ-500 |
Max loading weight | 100kg | 200kg | 300kg | 500kg |
Radius of gyration | 400mm | 400mm | 500mm | 600mm |
First axis Rotating speed | 80°/s | 80°/s | 60°/s | 50°/s |
Second axis Rotating speed | 80°/s | 80°/s | 80°/s | 50°/s |
Repeatability | ±1.0arc/m | ±1.0arc/m | ±1.0arc/m | ±1.5arc/m |
First axis Rotating angle | ±90° | ±90° | ±90° | ±90° |
Second axis Rotating angle | ±360° | ±360° | ±360° | ±360° |
Eccentricity | <=150mm | <=120mm | <=100mm | <=100mm |
Center of gravity | <=150mm | <=120mm | <=100mm | <=100mm |
PV Reducer | 40E-121 | 40E-121/80E-153 | 40E-121/110E-161 | 80E-153/110E-161 |
Servo motor | 0.75KW/1.0KW | 1.0KW/1.5KW | 1.5KW/1.5KW | 1.5KW/2.0KW |
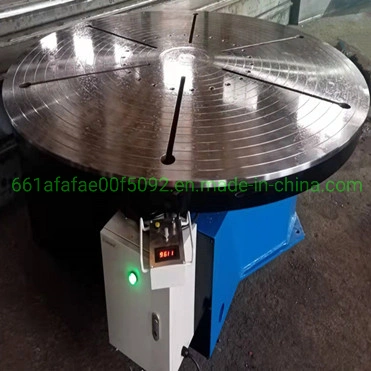
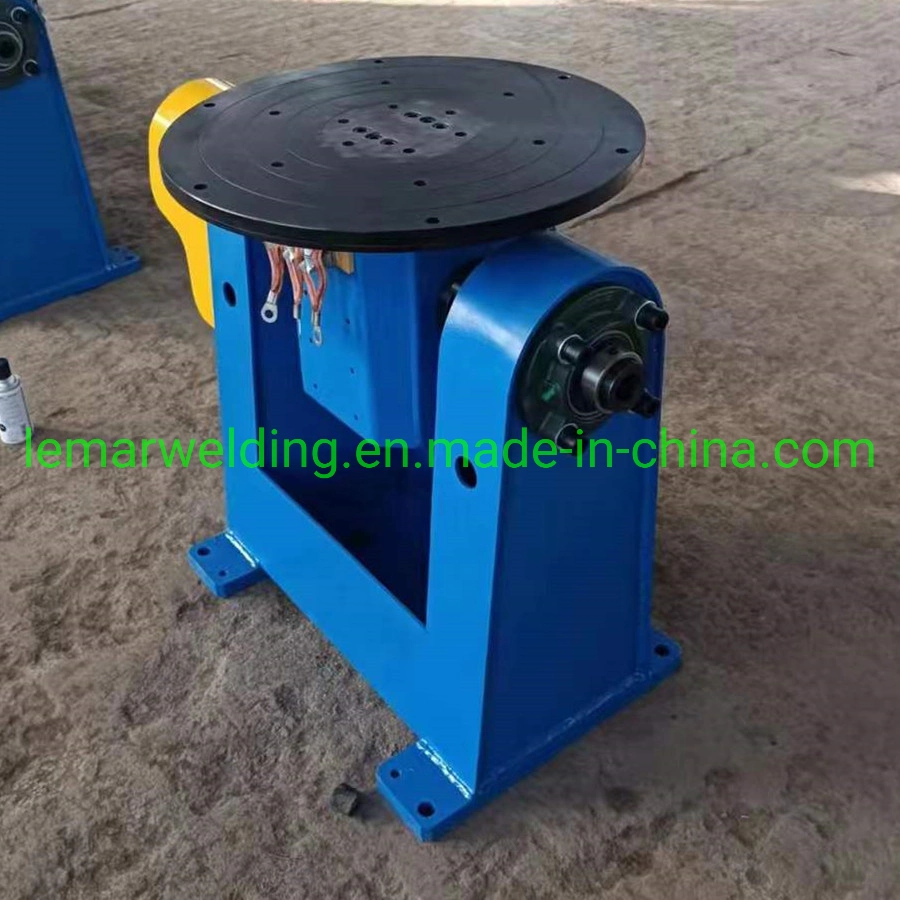
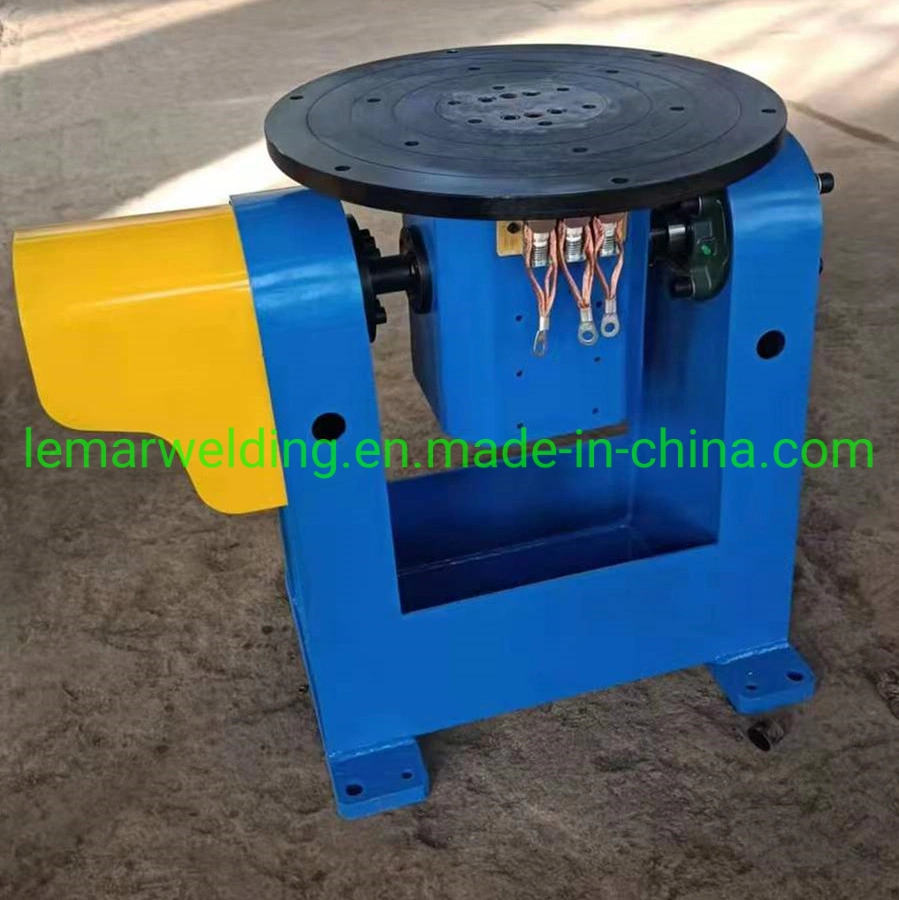
The advantages of the robot dual-axis dual-support positioner:
1. The automatic turning robot P-type double-axis welding positioner adopts a large platform to perform butt welding of welding components, which ensures the accuracy of the assembly.
2. After the welding of large welded components, the stress relief operation is performed to ensure that the welding components of the positioner will not be deformed when used for a long time.
3. It is processed by a large CNC machining center, and the processing surfaces of each position are completed in one clamping, which ensures the parallelism, perpendicularity and symmetry of the parts and components. Ensure the coaxiality and rotation accuracy requirements of the positioner.
4. The electrical control system uses well-known domestic brands to control the positioner, with stable performance and low failure rate. The electrical components are selected from well-known brands at home and abroad to ensure the quality and stability of use.
1. The automatic turning robot P-type double-axis welding positioner adopts a large platform to perform butt welding of welding components, which ensures the accuracy of the assembly.
2. After the welding of large welded components, the stress relief operation is performed to ensure that the welding components of the positioner will not be deformed when used for a long time.
3. It is processed by a large CNC machining center, and the processing surfaces of each position are completed in one clamping, which ensures the parallelism, perpendicularity and symmetry of the parts and components. Ensure the coaxiality and rotation accuracy requirements of the positioner.
4. The electrical control system uses well-known domestic brands to control the positioner, with stable performance and low failure rate. The electrical components are selected from well-known brands at home and abroad to ensure the quality and stability of use.
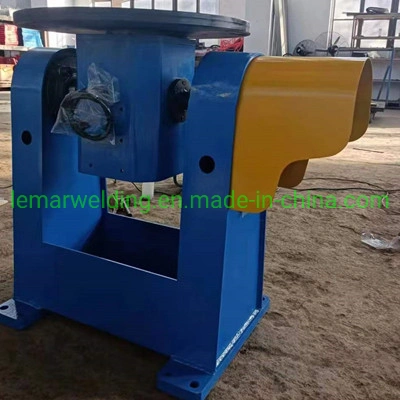
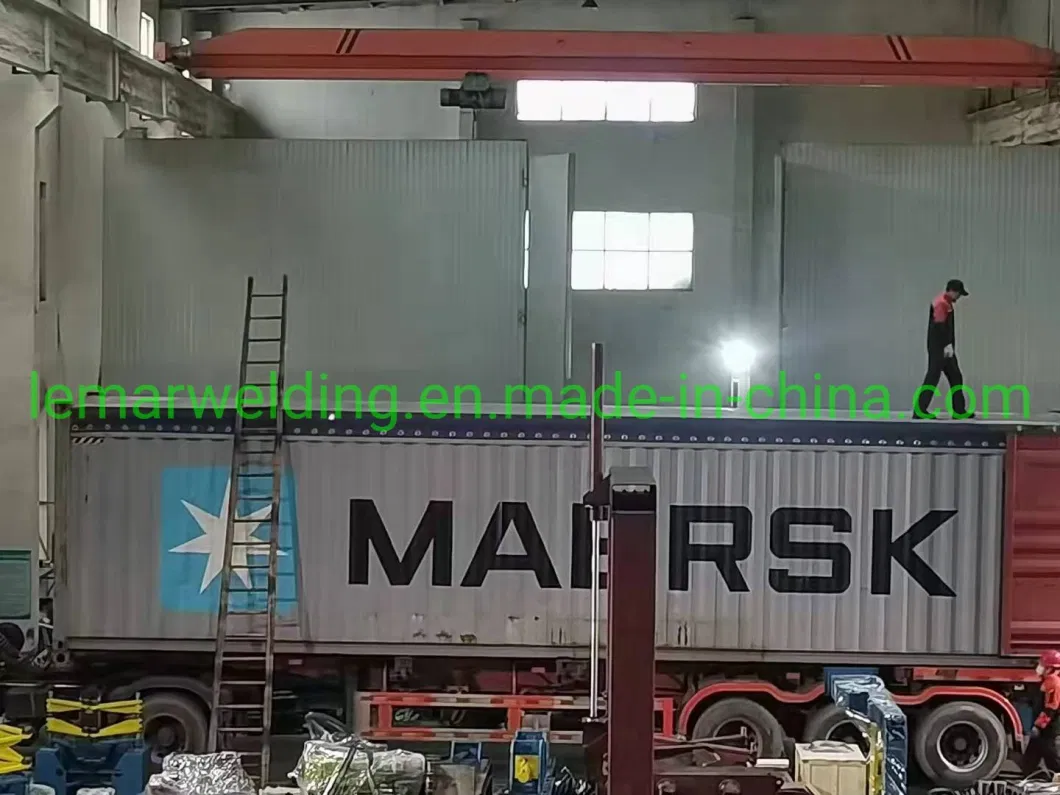
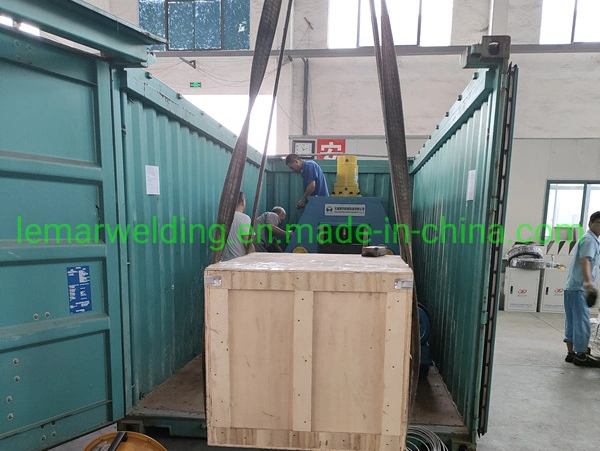